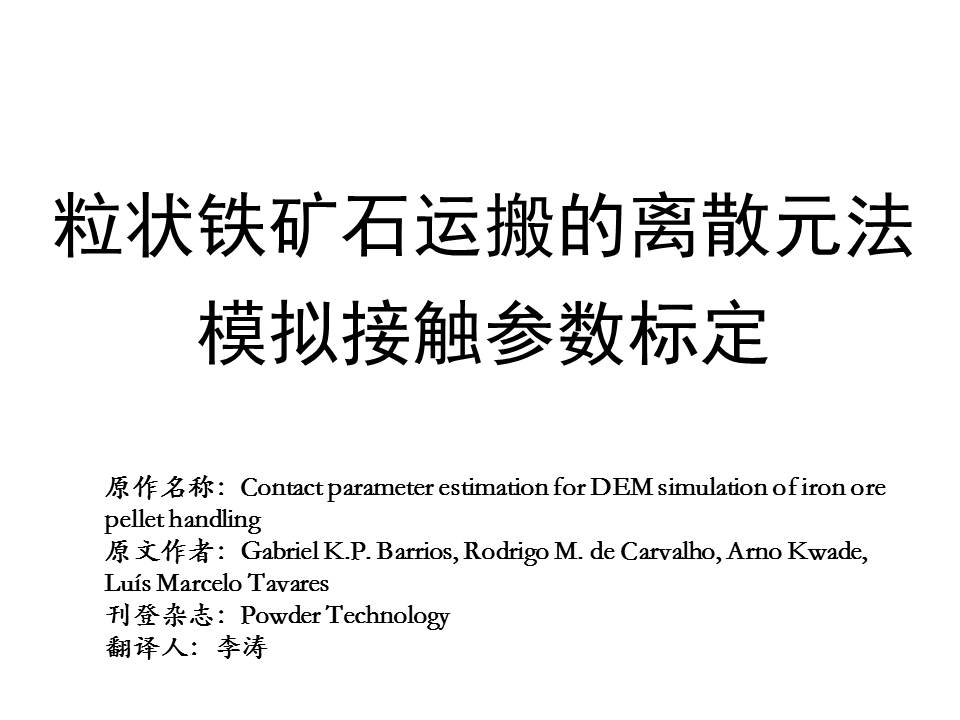
摘要 在利用离散元方法进行模拟时合适的接触参数对于整个模拟结果有着非常重要的意义,特别是在模拟类似铁矿石颗粒这种需要记录颗粒间的碰撞数据时,接触参数的选择显得尤为重要。本文利用单个矿石颗粒测试对离散元模拟中非滑动Hertz–Mindlin模型的接触参数进行了分析,测试方法主要有颗粒荷载碰撞、摩擦力测试、下降测试及单个颗粒的转动角测试。测试结果表明:试验选用的颗粒形状是适用于模拟的;基于单个颗粒测试的离散元模拟可以提供合理的接触参数预测值,并且在这种情况下接触参数是具有现实的物理意义的。如果仅以球形颗粒进行模拟将不能使模拟结果与试验结果相匹配,另外纯粹的为使接触参数与测试结果相匹配则会造成部分参数失去物理意义。
1. 引言
应用离散元法需要提供一系列材料参数,包括材料的碰撞性能及材料间的接触参数等,而这些参数需要提前测得材料的密度、尺寸、形状、剪切模量等来获取。在离散元模拟中最常用的接触模型为Hertz–Mindlin模型,该模型主要用来表述颗粒间的相互作用情况。在这个模型中最重要的参数就是碰撞恢复系数、静摩擦系数和滚动摩擦系数。
在固体形状不规则的情况下,Grima和Wypych等利用流动度试验等手段来推断材料参数。
直接还原炼铁法,是将矿石在固态下用气体或固体还原剂还原,在低于矿石熔化温度下,炼成含有少量杂质元素的固体或半熔融状态的海绵铁、金属化球团或粒铁,作为炼钢原料。尽管铁矿石球团有着比较高的强度,但在直接还原炉内转运过程中仍会受到撞击和磨损,因此很有必要对此进行研究。
离散元法可用于模拟铁矿石球团在转运过程中的degradation,但为了保证模拟效果,必须选择合适的碰撞参数。
2. 非滑动Hertz–Mindlin模型的接触参数
3. 试验方法
3.1 物理特性测试
试验所用的铁矿石球团来自巴西的某一工厂,颗粒尺寸从8到19mm不等,平均粒径d50为12.3mm。颗粒形状如图1所示。试验所用的颗粒通过筛分粒径均控制在9.0~12.5mm之间,颗粒密度通过比重瓶法测得。为表述颗粒形状通过二维图像来计算类球性(比值越接近1越近似球形)和长宽比L/W。
试验所用的铁矿石球团来自巴西的某一工厂,颗粒尺寸从8到19mm不等,平均粒径d50为12.3mm。颗粒形状如图1所示。试验所用的颗粒通过筛分粒径均控制在9.0~12.5mm之间,颗粒密度通过比重瓶法测得。为表述颗粒形状通过二维图像来计算类球性(比值越接近1越近似球形)和长宽比L/W。
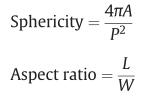
A—面积,p—周长。
颗粒的力学性能受加载速度的影响。材料的剪切模量G与杨氏模量E的关系为
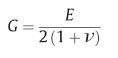
v—泊松比
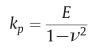
颗粒刚度kp
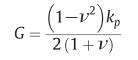
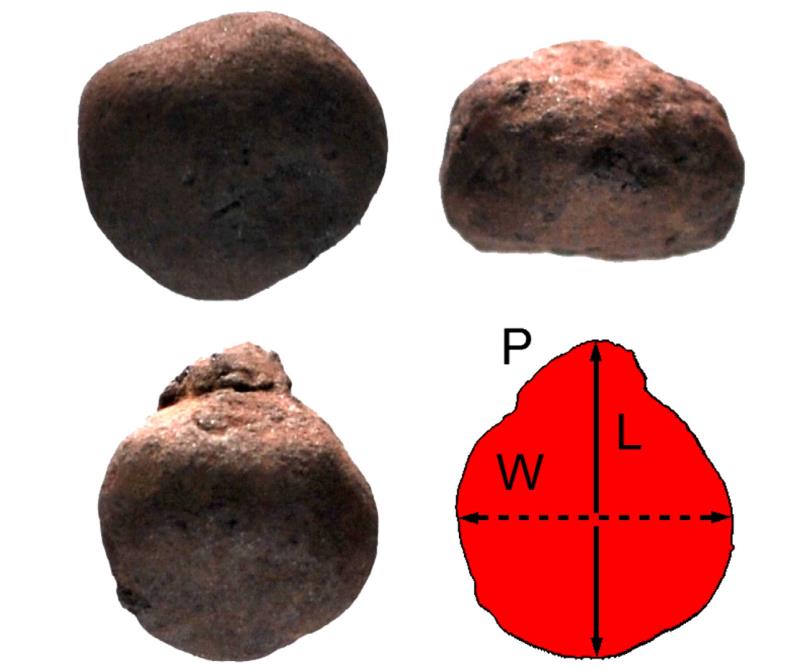
图1 铁矿石颗粒图像及图形分割示意(右下)
3.2 接触参数测试
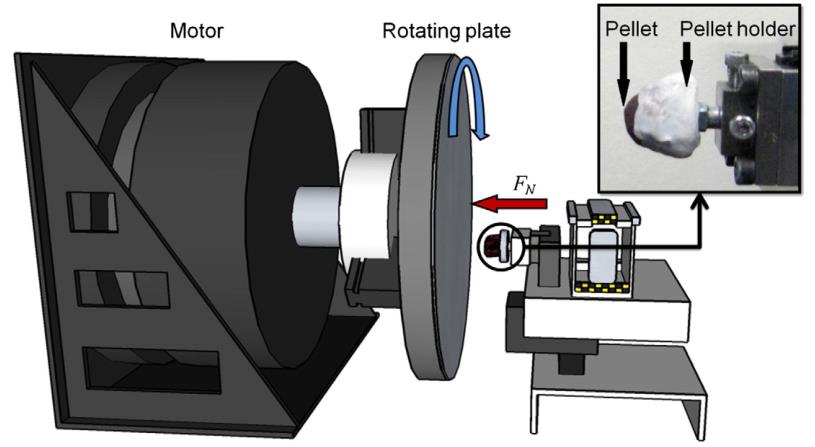
图2 用于测摩擦系数的Pin-on disk 摩擦计
转盘表层可以使用不同种类的接触材料。在本试验中,因为需要模拟的是铁矿石颗粒与颗粒之间的接触情况,试验前先在圆盘上涂上薄层树脂,然后再将铁矿石碎屑洒在上面。
静摩擦系数us通过切向力Ft与Fn计算:

试验测得法向力在10~50N之间,转盘速度在0.1~1.0m/s之间。
滚动摩擦力(外摩擦角)通过图3装置测得。试验时总共使用了30个铁矿石颗粒,随机的洒在试验板上,随后以不同角度调整试验板,直到颗粒开始向下滚动,记录该角度值。
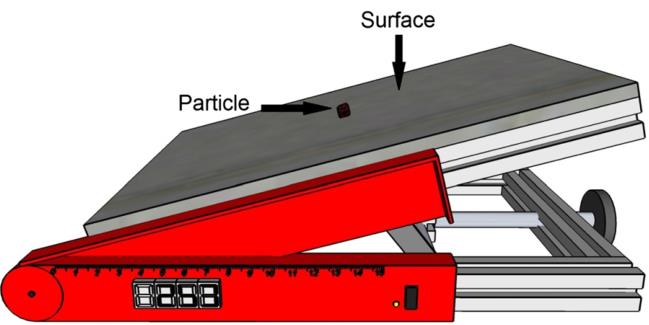
图3 钢板与铁矿石颗粒间滚动摩擦力测量装置
颗粒的碰撞恢复系数是通过图4装置进行测试。
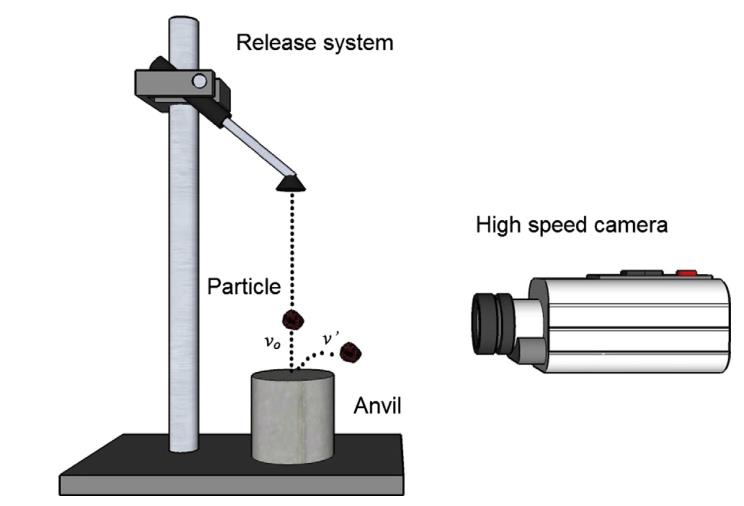
图4 用于测试v´/ v0的高速记录系统
颗粒由真空释放机放出,在重力作用下落在底部的铁毡上,整个过程由高速摄影仪(200帧/秒)记录下来。颗粒的碰撞后速度v´与碰撞前速度v0比值可以计算出来(碰撞前后各5帧,0.025s的时间跨度)。
3.3 验证试验
现在要解决这样一个问题:单个颗粒的测试结果能否应用于离散元模拟中的整体流动情况?
自然安息角是通过塌落筒试验测得的。将直径为97mm的塌落筒提起,里面12kg的铁矿石颗粒将堆积在底部的钢板上。
4. 试验结果分析
4.1 颗粒物理特性
在之前的研究中,重叠球体模型被广泛应用于形状不规则颗粒的模拟。研究表明,重叠球数量越多,模拟结果与实际效果越相似,但计算量会相应增加。目前一般取3~4个。
图5对三种铁矿石颗粒进行了比较,其中重叠球体模型的类球性为0.90。
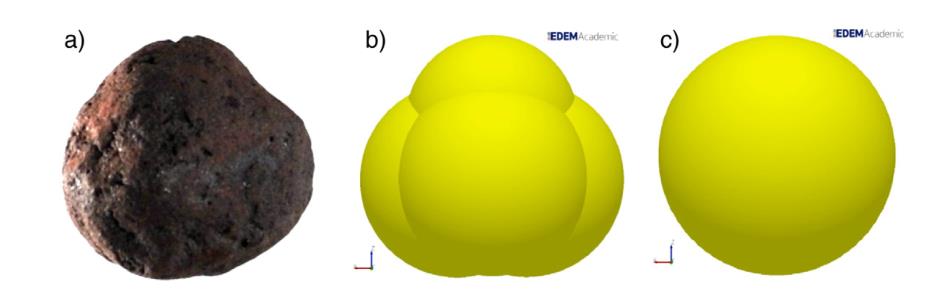
图5 铁矿石颗粒a)实体图 b)重叠球体模型 c)球体模型
颗粒表面的粗糙度对模拟结果有着至关重要的作用,主要对静摩擦系数有着直接影响。
表3 单个颗粒属性
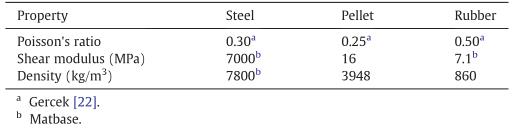
4.2 接触参数
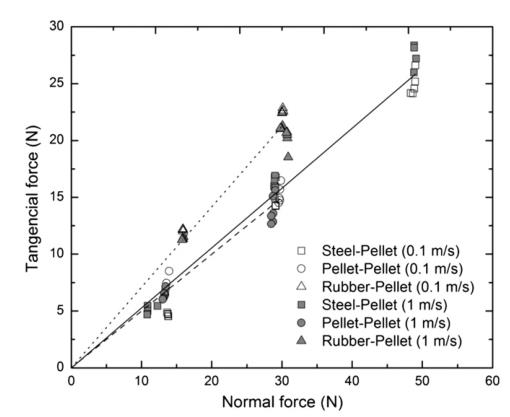
图6 pin-on-disk摩擦试验曲线
图6为pin-on-disk摩擦试验不同相对速度、法向力及表面类型。摩擦系数us是过原点的直线,研究结果证明相对速度和法向力对摩擦系数没有影响,但表面材料对其有重要的影响作用(表4)。
表5 单个颗粒试验接触参数汇总
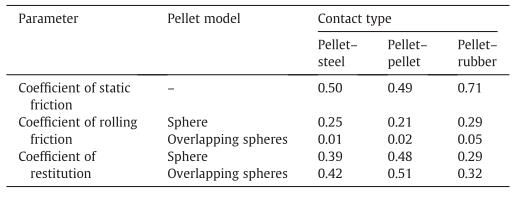
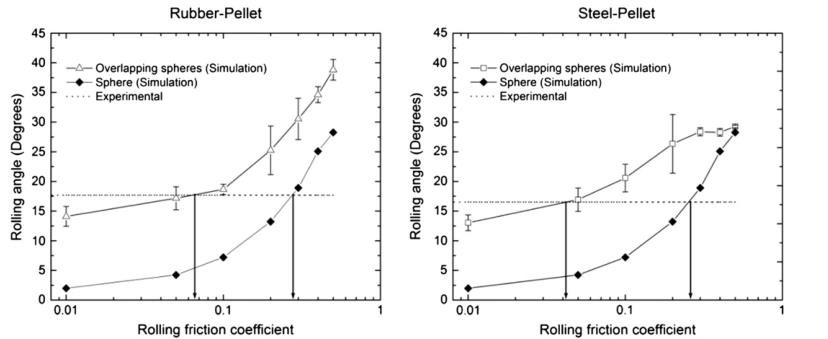
图7 DEM模拟的不同外摩擦角与试验结果对比曲线
颗粒模型为球体时,为获得较准确的模拟结果需要人为将滚动摩擦系数调为0.2~0.3。
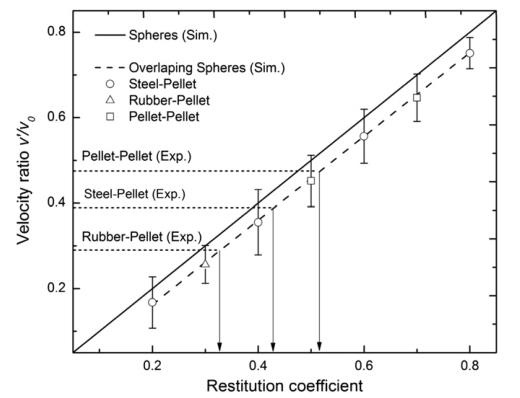
图8 DEM模拟的不同碰撞恢复系数的速度比与试验结果对比曲线
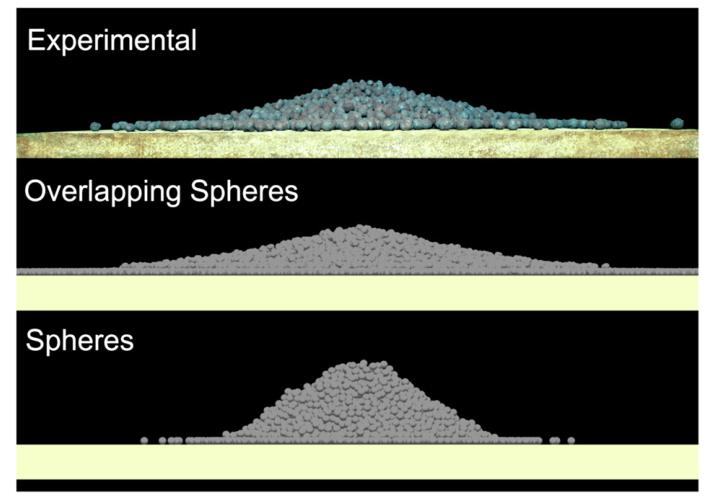
图9 现实塌落试验(上)与模拟(中、下)塌落试验对比(钢板)
4.3 验证
5. 结论
单个颗粒的测试结果可用于DEM模拟中的接触参数标定,并且不需要大量的计算工作。
在模拟过程中,铁矿石颗粒模型形状越接近原型,准确性会越高;如果仅为简单的球形模拟,则模拟效果的准确性不确定。只有在静摩擦系数减小的情况下现实试验和模拟试验的结果才能取得一致。